Nationwide Engineering
for Commercial and Utility Scale solar + Storage Projects
Solar & Energy Storage Design Engineering Services
%20(1).png)
Value Engineering Tips | Solar + Storage See More
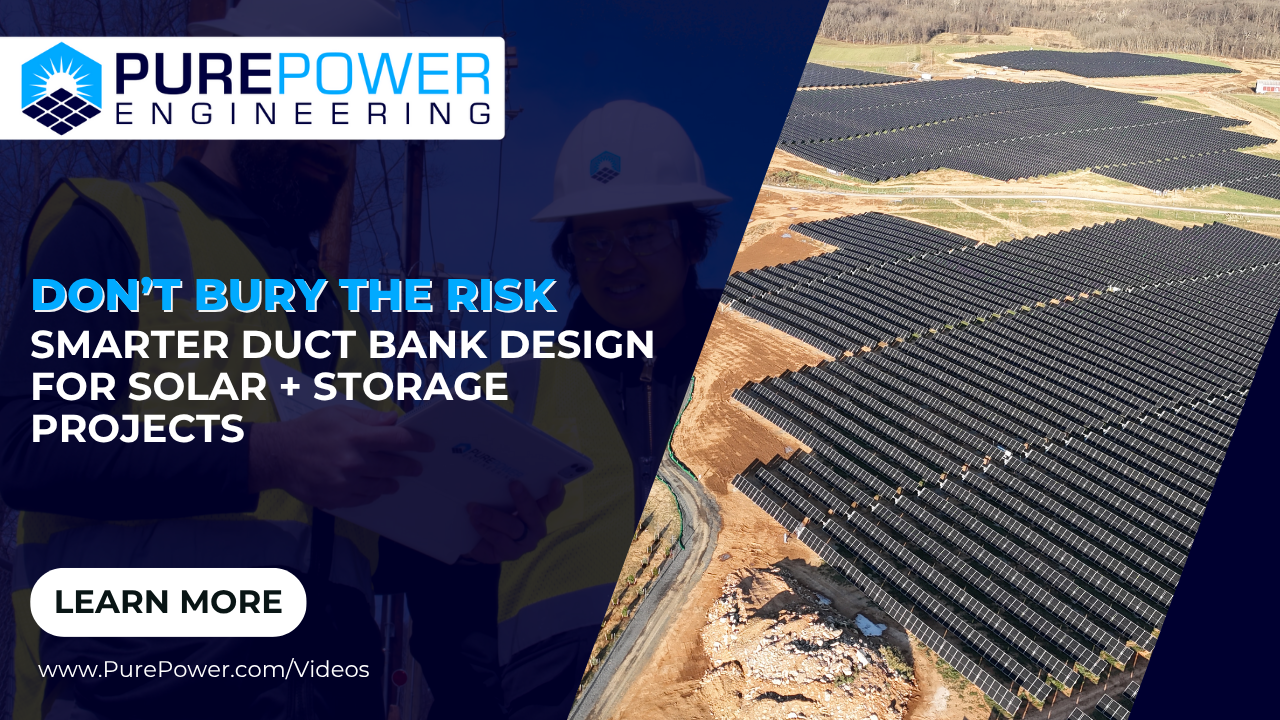
Don’t Bury the Risk: Smarter Duct Bank Design for Solar + Storage Projects
Overheating cables. Faults before PTO. Trench rework. That’s what happens when duct bank design is an afterthought. At Pure Power, we don’t just draw trench lines—we run detailed duct bank studies that simulate real-world heat loads, validate NEC..
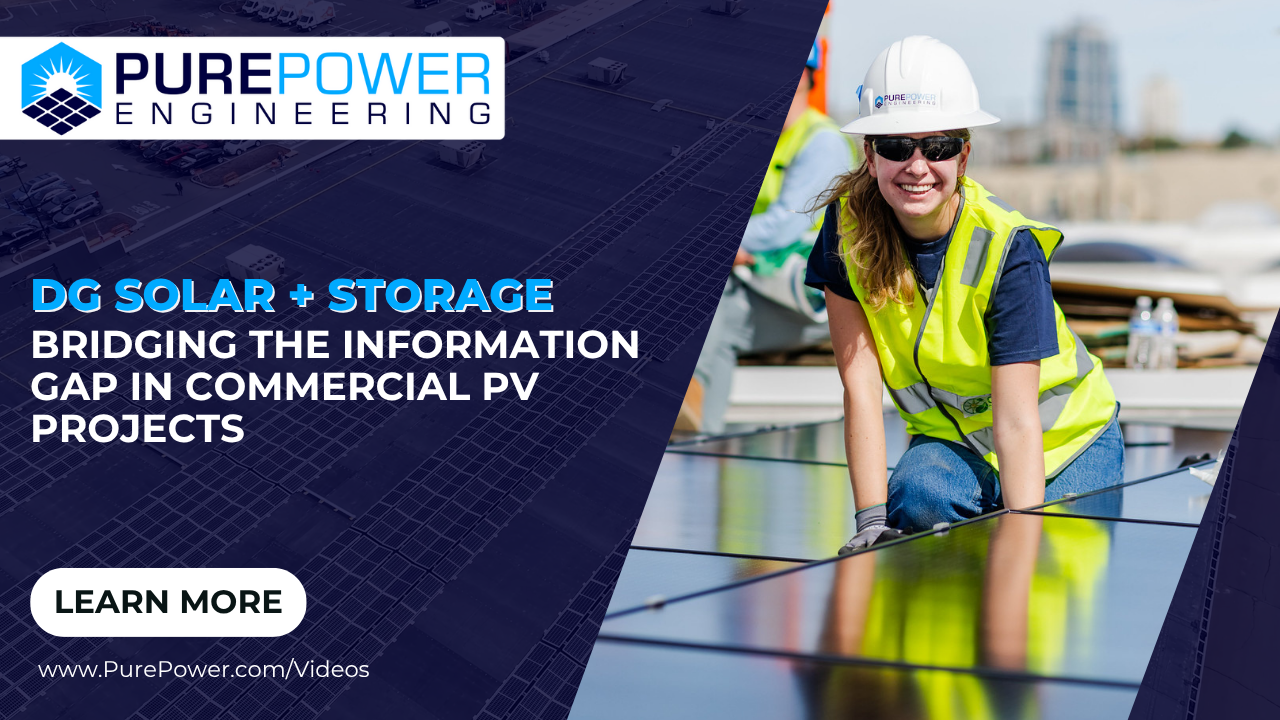
Bridging the Information Gap in Commercial PV Projects
Delays in Commercial PV Projects? It's Usually Not the Equipment—It's the Information. In commercial solar + storage projects, delays don’t just cost time—they derail budgets, damage investor confidence, and ripple all the way through procurement..
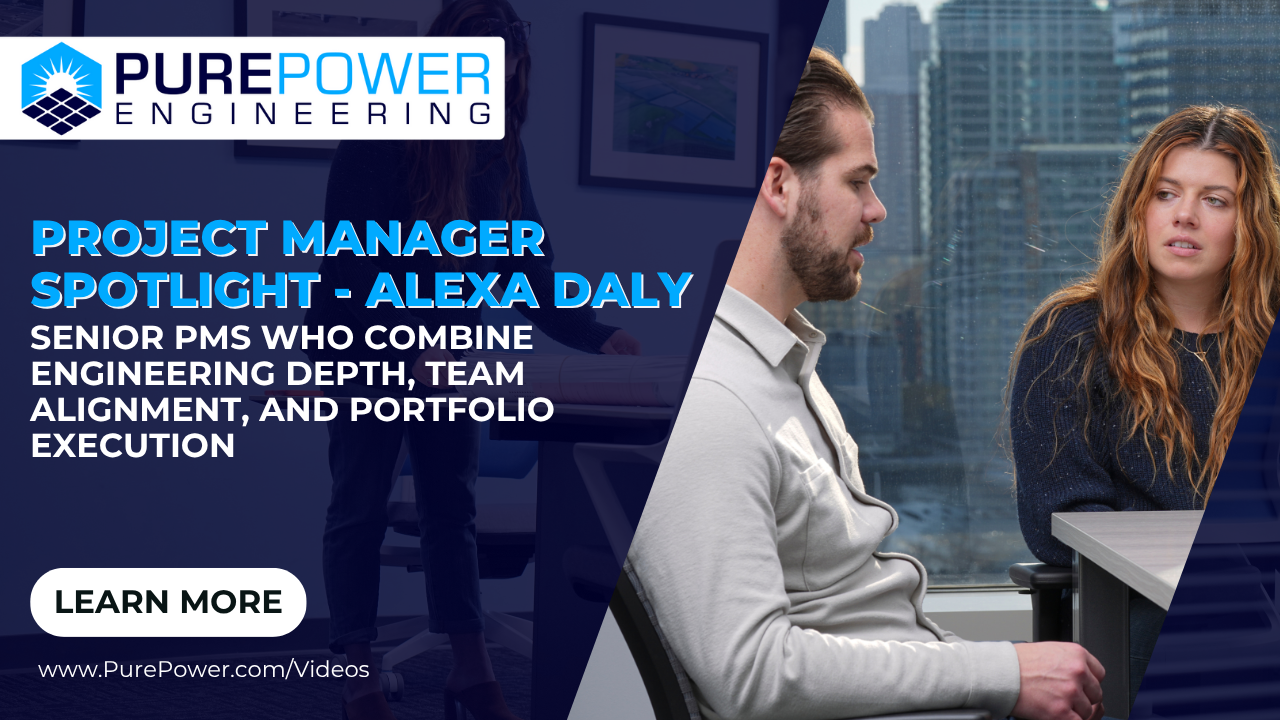
Senior PMs Who Combine Engineering Depth, Team Alignment, and Portfolio Execution
At Pure Power, our PMs didn't just become leaders—they earned it from the ground up. Alexa Daly shares how every Project Manager started in the trenches as a project engineer, building the technical chops that make them exceptional managers today...
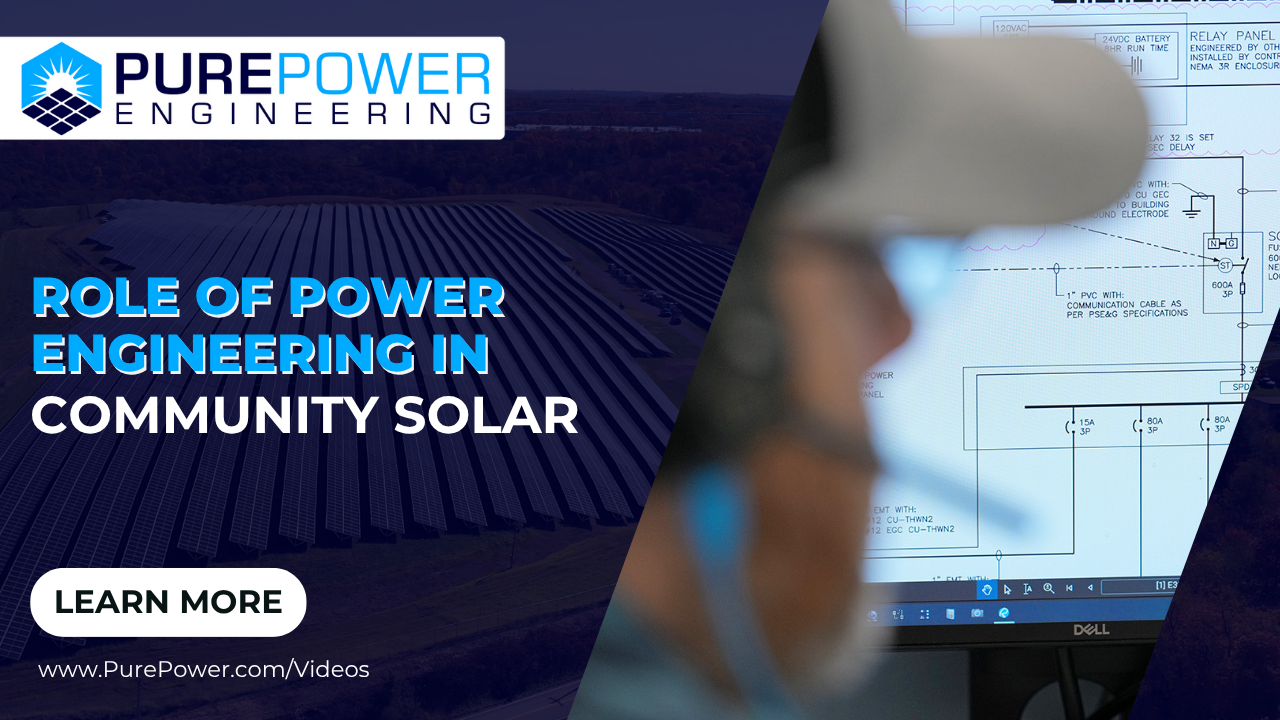
The Role of Power Engineering in Community Solar Projects
Community Solar Doesn’t Connect Without Proper Power Engineering | These 1–5 MW ground mount systems may look small—but they’re held to utility-scale level standards. From MV design and power studies to utility coordination, we ensure every..
At Pure Power Engineering, we are at the forefront of transforming the renewable energy landscape in the United States. Specializing in solar power and cutting-edge design services, our team excels in electrical solar design engineering to deliver top-tier solutions. Our solar energy engineers work tirelessly on energy storage projects, ensuring that every solar-designed system we create meets the highest standards of efficiency and reliability. Through meticulous feasibility studies, we guarantee that our solar energy systems are seamlessly integrated into existing power systems. Whether it's large-scale solar energy projects or tailored renewable energy solutions, our engineers work diligently to provide innovative, sustainable, and effective power solutions. Choose Pure Power Engineering to harness the full potential of solar power and drive the future of renewable energy.
Contact Us
The Latest from Pure Power View All
Disconnect switches are often overlooked in the planning and installation of commercial PV systems—until they result in cost overruns, code compliance issues, or safety hazards. During a recent roundtable of Pure Power's senior projects managers...
Continue Reading →Distributed solar generation continues to accelerate. According to SEIA, the US added 50 gigawatts of new solar in 2024, with commercial solar growing 8% yearly. However, the path to electrification is increasingly shaped by two critical hurdles:...
Continue Reading →Well-executed utility-scale solar projects follow a specific pattern, allowing for completion on time and without additional cost. Arguably one of the most critical factors in the development is managing the intersection of electrical, civil, and...
Continue Reading →